{{ pageName }}
Flame Retardant Material with Superior Performance Based on GRS
(GRS flame-retardant nonwoven fabric)
Distinguished for their excellent flame resistance and are formulated from 100% recycled, eco-friendly materials.
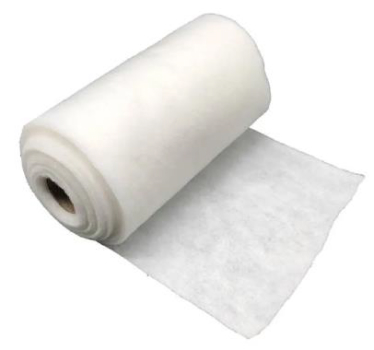
Product Introduction
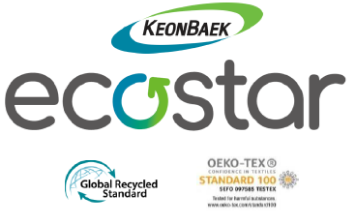
Recycled Polyester
From Post-consumer Waste
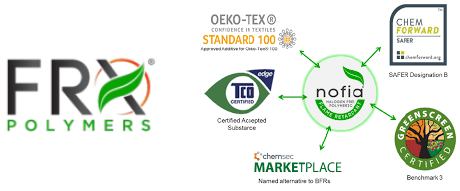
Non-halogenated
Flame Retardant

Section | Value |
---|---|
Denier(De’) | 3~6 |
Length(mm) | 22~64 |
P Contents(ppm) | 6,000~10,000 |
Note | Permanent Type |
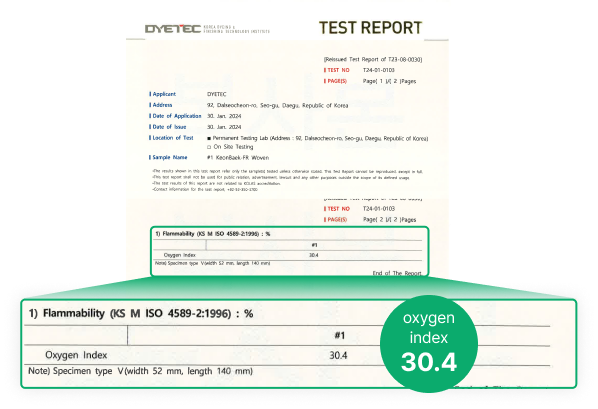
LOI TEST Report
LOI Value 30 ↑ (at P Content 6,000 ppm)
Eco-friendly Material
Eco-friendly Phosphorus-based Flame Retardant Material based on GRS
Produced using the Global No.1 process that requires the lowest energy consumption and carbon emissions among PET recycling methods. Compared to the virgin process, it achieves an 86% reduction in Non-Renewable Energy Use (NREU) and a 76% reduction in Global Warming Potential (GWP) emissions.
-
Crude Oil Extraction
Landfill/Incineration
Reduction in energy used for the extraction and refining of crude oil and a decrease in greenhouse gas emissions during the disposal phase.
-
PET bottle
rPET
FlakerPET
FiberResource Recovery from Waste Plastic
Production of eco-friendly fiber products using waste PET bottles as raw materials, contributing to the reduction of greenhouse gas emissions.
Phosphorus-based Flame Retardants
Transition from Halogen-Based to Phosphorus-Based Flame Retardants
Traditional halogen-based flame retardants are being restricted in various regulatory frameworks such as the European RoHS directive due to their adverse health effects, including dizziness, visual impairments, headaches, abdominal pain, disorientation, and hallucinations. There's a growing trend to replace these with non-halogenated products.
Intensifying Regulations Due to Environmental Stability Concerns: Halogen-Based Flame Retardants
These flame retardants work by trapping active OH and H radicals with radical HX, leading to stabilization. HX is non-flammable and works by dilution and by blocking oxygen, thus manifesting its flame-retardant properties.
However, during injection molding, these substances can release gases, and during incineration, they can produce environmentally harmful dioxins. They are also associated with severe soot and smoke generation due to aromatic hydrocarbons.
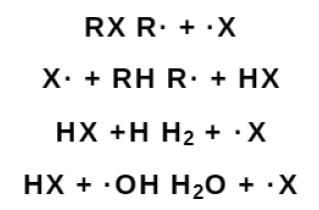
Replacement with Non-Halogenated Products: Phosphorus-Based Flame Retardants
In the gas and condensed phases, the simultaneous interaction leads to the manifestation of flame-retardant effects through the dehydration and carbonization caused by the thermal decomposition of phosphoric acid, as well as the scavenging of hydrogen and hydroxyl radicals by phosphorus-containing radicals.
Formation of char and phosphoric layers: During combustion, the formation of char is facilitated, creating an incombustible layer on the surface that physically obstructs the internal heat transfer within the polymer resin.
Flame retardant mechanism in the gas phase: Through pyrolysis, radicals such as PO2· are generated. This mechanism, similar to that of halogen-based flame retardants, captures hydrogen and hydroxyl radicals, forming a flame-retardant mechanism in the gas phase.
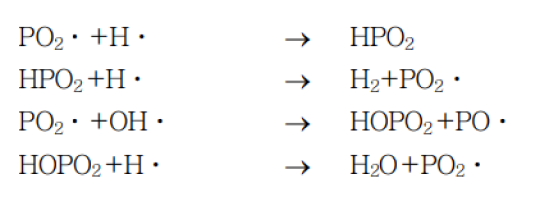
Manufacturing process
Needle-punched nonwoven fabric manufacturing process
-
Flame Retardant, GRS R-PET Staple Fiber
-
Needle Punching Non-woven process
-
GRS FR Needle Punching Non-woven
Application fields
Application fields of Needle-punched nonwoven fabric
-
Artificial leather
-
Floor carpet
-
Head liner